Securing Industrial Control Systems (ICS) in the Age of Industry 4.0
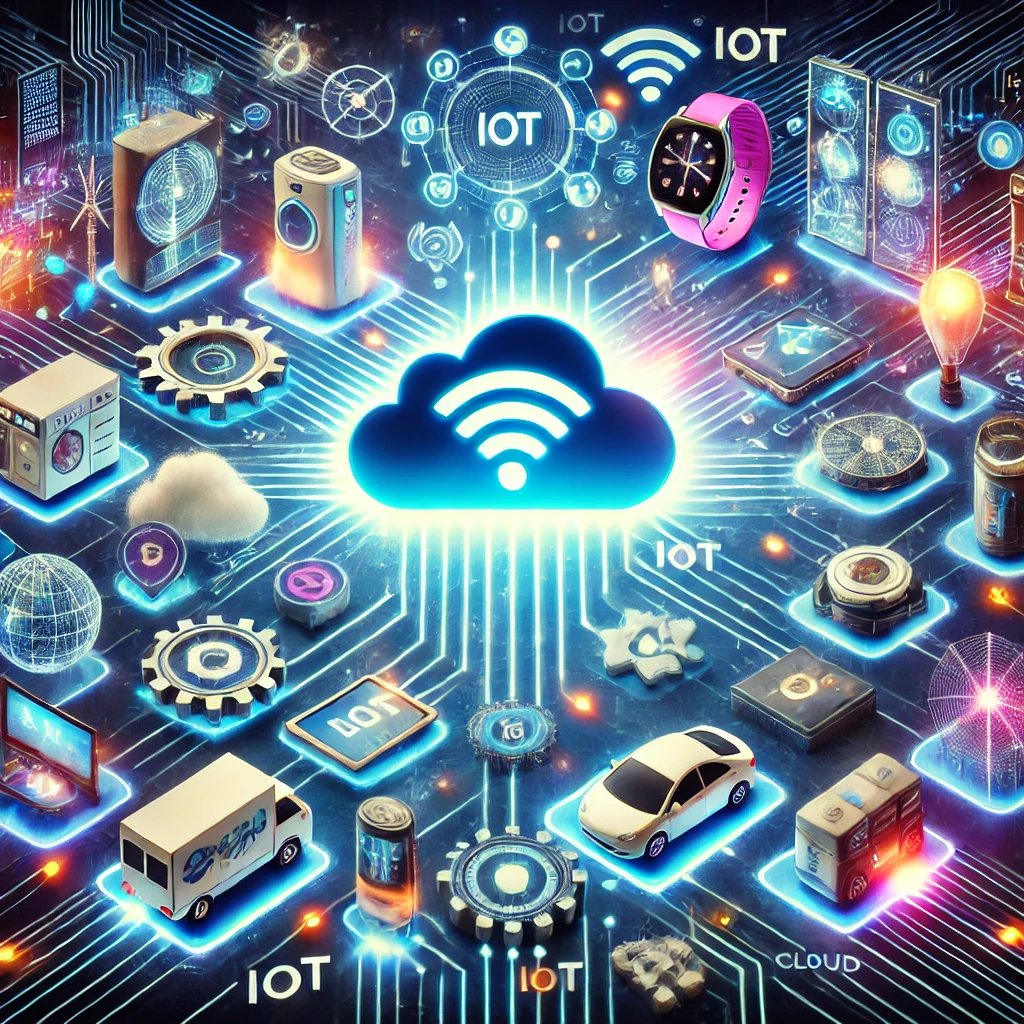
Categories:
7 minute read
In the rapidly evolving landscape of industrial technology, the convergence of operational technology (OT) and information technology (IT) has ushered in a new era known as Industry 4.0. This digital transformation promises unprecedented levels of efficiency, productivity, and innovation in industrial processes. However, it also brings with it a host of new security challenges, particularly in the realm of Industrial Control Systems (ICS). As we embrace the benefits of industrial IoT and smart manufacturing, ensuring the security and integrity of these critical systems has never been more crucial.
Understanding Industrial Control Systems (ICS)
Before delving into the security challenges and solutions, it’s essential to understand what Industrial Control Systems are and their significance in modern industry.
What are Industrial Control Systems?
Industrial Control Systems are networks of interconnected components used to monitor and control physical processes in industrial environments. These systems are crucial in managing everything from power generation and water treatment to manufacturing and transportation.
Key components of ICS include:
Supervisory Control and Data Acquisition (SCADA) systems: These provide centralized monitoring and control for large-scale processes.
Programmable Logic Controllers (PLCs): Rugged computer devices that control industrial processes.
Human-Machine Interfaces (HMIs): Interfaces that allow human operators to interact with and monitor the ICS.
Sensors and actuators: Devices that measure physical properties and control industrial equipment. The Evolution of ICS in Industry 4.0
The advent of Industry 4.0 has dramatically transformed traditional ICS:
Increased connectivity: ICS are now connected to corporate networks and the internet, enabling remote monitoring and control.
Cloud integration: Many ICS now leverage cloud computing for data storage and analysis.
Industrial Internet of Things (IIoT): The proliferation of smart sensors and devices has created a vast network of interconnected industrial equipment.
Big Data and AI: Advanced analytics and artificial intelligence are being used to optimize industrial processes and predict maintenance needs. While these advancements offer significant benefits, they also expand the attack surface for potential cyber threats.
The Security Challenges Facing ICS in Industry 4.0
The integration of IT and OT in Industry 4.0 has introduced several security challenges:
- Expanded Attack Surface
As ICS become more connected, they become more vulnerable to cyber attacks. The attack surface now extends beyond the physical plant to include remote access points, cloud services, and even third-party vendors.
- Legacy Systems
Many industrial environments still rely on legacy systems that were not designed with cybersecurity in mind. These systems often lack basic security features like encryption or authentication.
- Operational Constraints
Unlike IT systems, ICS often have strict operational requirements that can make traditional security measures challenging to implement. For example, patching systems may require shutting down critical processes, which can be costly and disruptive.
- IT/OT Convergence Challenges
The merging of IT and OT brings together two traditionally separate domains with different priorities, skill sets, and security approaches. This can lead to gaps in security coverage and miscommunication.
- Supply Chain Risks
As industrial processes become more interconnected, vulnerabilities in one part of the supply chain can have far-reaching consequences. Attackers may target smaller, less secure vendors to gain access to larger industrial networks.
- Lack of Visibility
Many organizations lack comprehensive visibility into their ICS environments, making it difficult to detect and respond to threats effectively.
The Threat Landscape for ICS
The threats facing ICS are diverse and evolving:
State-Sponsored Attacks
Nation-states may target critical infrastructure as part of broader geopolitical conflicts. Examples include the Stuxnet worm that targeted Iranian nuclear facilities and attacks on Ukraine’s power grid.
Ransomware
Cybercriminals are increasingly targeting ICS with ransomware, recognizing the high stakes involved in industrial operations. The Colonial Pipeline attack in 2021 highlighted the potential impact of such attacks.
Insider Threats
Disgruntled employees or contractors with insider knowledge can pose a significant risk to ICS security.
Unintentional Incidents
Human error, such as misconfiguration or accidental damage to systems, can also lead to security incidents in ICS environments.
Strategies for Securing ICS in Industry 4.0
Securing ICS in the age of Industry 4.0 requires a comprehensive approach that addresses both technical and organizational challenges:
- Implement Network Segmentation
Divide the ICS network into separate zones based on criticality and function. Use firewalls and other security controls to limit communication between zones and enforce the principle of least privilege.
- Conduct Regular Risk Assessments
Perform thorough risk assessments to identify vulnerabilities and prioritize security efforts. This should include both cyber and physical security considerations.
- Develop and Maintain an Asset Inventory
Maintain a comprehensive inventory of all hardware and software assets in the ICS environment. This is crucial for identifying vulnerable systems and managing patches effectively.
- Implement Strong Access Controls
Use multi-factor authentication, role-based access control, and the principle of least privilege to limit unauthorized access to ICS components.
- Enhance Monitoring and Incident Response
Deploy industrial-specific security information and event management (SIEM) solutions to monitor ICS networks for anomalies. Develop and regularly test incident response plans tailored to ICS environments.
- Secure Remote Access
As remote work becomes more common, ensure that remote access to ICS is tightly controlled and monitored. Use VPNs, jump servers, and other security measures to protect remote connections.
- Address Supply Chain Security
Implement rigorous vendor risk management processes. Conduct security assessments of third-party vendors and ensure they meet your security standards.
- Provide Cybersecurity Training
Offer regular cybersecurity training to all employees, including those in OT roles. This should cover both general cybersecurity best practices and ICS-specific security considerations.
- Implement Secure-by-Design Principles
When upgrading or implementing new ICS components, choose vendors and products that prioritize security in their design. Look for features like secure boot, encrypted communication, and robust authentication mechanisms.
- Develop a Patch Management Strategy
Create a patch management process that balances security needs with operational constraints. This may involve testing patches in a staging environment and scheduling updates during planned downtime.
The Role of Standards and Regulations
Several standards and regulations have been developed to guide ICS security efforts:
NIST Special Publication 800-82: Provides guidance on securing Industrial Control Systems.
IEC 62443: A series of standards for industrial communication networks and system security.
NERC CIP: Mandatory cybersecurity standards for the North American electric utility industry. Organizations should familiarize themselves with relevant standards and regulations and incorporate them into their security programs.
Future Trends in ICS Security
As Industry 4.0 continues to evolve, several trends are likely to shape the future of ICS security:
AI and Machine Learning
Advanced analytics and machine learning algorithms will play an increasingly important role in detecting and responding to threats in ICS environments.
Zero Trust Architecture
The zero trust security model, which assumes no user or device should be trusted by default, is likely to gain traction in ICS environments.
Quantum-Safe Cryptography
As quantum computing advances, ICS security solutions will need to incorporate quantum-resistant encryption methods to protect against future threats.
Edge Computing Security
As more processing moves to the edge in ICS environments, new security solutions will be needed to protect these distributed computing resources.
Conclusion
Securing Industrial Control Systems in the age of Industry 4.0 is a complex but critical challenge. The convergence of IT and OT, coupled with the increasing connectivity of industrial processes, has created new vulnerabilities that must be addressed. However, by adopting a comprehensive approach to security that encompasses technology, processes, and people, organizations can harness the benefits of Industry 4.0 while minimizing the associated risks.
As we move forward, it’s clear that ICS security will require ongoing attention and adaptation. The threat landscape will continue to evolve, and new technologies will introduce both opportunities and challenges. Organizations that prioritize ICS security, stay informed about emerging threats and best practices, and foster a culture of security awareness will be best positioned to thrive in the digital industrial future.
By securing our Industrial Control Systems, we’re not just protecting individual organizations – we’re safeguarding the critical infrastructure that underpins our modern society. In the age of Industry 4.0, ICS security is more than just a technical challenge – it’s a fundamental requirement for sustainable industrial progress.
Feedback
Was this page helpful?
Glad to hear it! Please tell us how we can improve.
Sorry to hear that. Please tell us how we can improve.